|
 |
协同产生创新,创新产生价值 |
作者: 鲁君尚 来源于: 2003-6-6 16:16:03 |
|
|
|
|
|
制造业企业信息化的目标,首先是向产品要效益,同时也要努力向管理要效益,归根结底是要通过“协同”向“创新”要效益。 制造业企业的信息化应用场景
M公司是一家专业从事某领域产品开发与生产制造的典型制造业企业。为争取到为上游厂家A公司配套的X产品订单,M公司专门组建了由销售部门与新产品开发部门等相关人员参与的项目组,负责与A公司相关人员进行该X产品的技术沟通及商务洽谈。 项目组根据A公司提供的X产品的技术要求、规格说明、相关图纸、三型模型等技术资料,经过多次频繁地往来沟通,大量参阅了业内相关企业同类产品的最新设计方案,最后在M公司北美机构的某一已有型号方案X0(全套图纸及三维型等)基础上,融入M在X产品方面的先进设计理念与丰富经验,经过改型完成初步设计,很快向A公司提交了该X产品方案,包括动态三维模型(电子样机)、主要技术指标、生产制造计划及价格等,从而在多家公司竞争的条件下,顺利争取到了A公司的X产品订单。 订单就是任务、就是计划。M公司立即就X产品立项,构建X产品项目管理体系;同时由新产品开发中心负责组织X产品的设计工作。 新产品开发中心按照与A公司共同确定的X技术规格与初步方案,经过进一步深入分析和计算,从网络数据库中调出X0全套图纸、三维模型等已有技术资料,通过局部改型,迅速确定了X的系统结构方案,完成整体设计。因为利用了M在该产品领域积累的丰富、强大的构件库、标准件库、知识库和经验库等,通过知识重用,X的开发设计工作量和工作难度被大大减小。围绕少数关键零部件的详细设计工作,从三维设计到工程出图,很快在全中心大面积同时展开。 在设计过程中,M北美机构的两位资深工程师也理所当然地加入了项目。整个X产品项目借助网络提供的版本、权限、数据接口与沟通交流等等协同功能,顺利实现了异地的网络化协同设计,并且还方便地响应了设计过程中A公司对X产品技术要求的多次变更。 在完成X的三维建模、工程设计的同时,通过CAX集成,直接读取零件的三维数模,对X关键件进行了有限元分析、校核等等工程分析,并快速完成了X产品的全部设计工作。 产品设计完成后,迅速转入生产工艺设计与工装设计等生产前准备阶段。通过CAX集成,直接从网络数据库读取产品的设计模型与图纸,进行生产工艺规划、工艺汇总、生产计划编制、生产成本定额编制等,确定标准件、外购件与自制件,并对自制件的制造模具以及产品组装卡具等工装准备进行设计,完成生产工艺规划。 产品开始生产之前,M公司组织相关门对X产品进行了全面审核,并对其设计与工艺部分地方进行了更正和改动。经过技术、经济与生产组织等方面的严格审核,X产品获准生产,并由公司向相关生产承担单位和部门发布X的技术与工艺文件(二维发图、零部件三维数模、工艺规程卡片、生产计划等),X产品进入生产实施阶段。 负责采购(或外协)的部门根据X产品的生产计划与技术要求,向下游厂家发布外购非标件,并开始标准件、外购件、原材料等的招标采购及其合理库存的计划管理工作。下游厂商N公司获得向M公司提供X产品配件的订单后,按照M公司提供的配件技术要求,直接读取图纸与三维模型,开始该配件的设计和制造工作。 M公司生产一部负责某自制关键件模具的制造工作。通过网络数据库,生产一部直接读取该模具的三维模型,根据该模具型腔及其曲面的特点,从以前积累的加工知识库中直接选取某相似件的加工套路模板,并结合加工设备的条件,对该模具的数控加工工艺参数作了适当改动,迅即完成了该模具的数控加工代码编制,经代码仿真检验无误后,通过网络DNC传给加工中心机床完成该模具的数控加工制造,并提交给下一道生产工序。 生产三部负责X产品的组装总成。在各零部件到位之前,三部技术人员先期通过网络调出各零部件模型在计算机上进行了多次模拟预装配,并根据模拟情况及公司发布的生产计划与工艺规划,对装配工艺做了进一步细化和优化,制作成X产品的组装流程三维动画片及各工位的工艺卡片以指导工人操作;同时通过网络协同,随时掌握各前道工序进展与配件库存情况,适时调整生产计划,控制生产成本,确保按时、按质、按量、低成本地完成X产品的生产。 X产品经严格的调试与成品检验合格后,即可按订单要求开始向A公司小批量供货。 M公司内各X产品相关部门还需要及时将X产品设计制造中经修改、验证的全套技术资料与经验、知识等进行整理、记录、汇总和存档,并对相关工模具等工装设备进行保养和维护,以避免“猴子扳棒”造成企业资源混乱而流失,实现技术积累和保密。 此后利用数据库中X产品的电子模型,相关部门容易地生成精美图片及形象的三维动画,制作成平面或多媒体的X产品安装和使用说明,随产品一同交付A公司;并且随着供货,M公司的X产品售后服务工作也便开始了,包括产品安装和使用中的故障问题、备件更换/更改等产品技术信息(图纸、三维模型等),就随同其他服务信息化一起,通过用户服务部门而在M公司的数据库中得到记录、沟通、开发和管理。 (制造业企业的信息化应用如图1所示。) 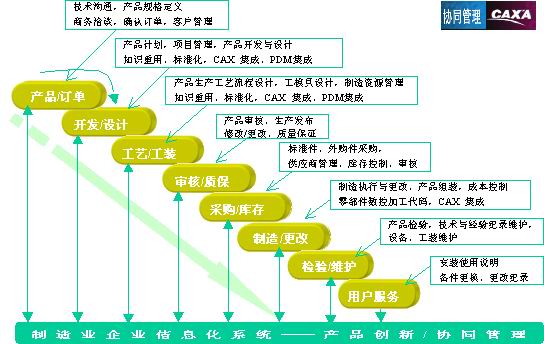 图1制造业企业信息化系统的应用——产品创新/协同管 |
| 产品创新是制造业企业的灵魂
产品是制造业企业的价值源泉;产品创新设计/制造是制造业企业所有工作的中心。 进入新的世纪以后,随着经济全球化和全球信息化的加速,全球制造业正在全方位广泛而深入地采用现代信息技术,制造模式与市场环境呈现新的特征: 产品生命周期越来越短、产品创新越来越快; 产品从设计、制造到交付用户的周期越来越短; 网络化、全球化优化资源配置,产品制造成本越来越低、品质更优良; 制造业企业内部及其与供应商、用户沟通与协作更方便,市场响应更快捷;等。 突出表现为产品创新更快、品质更优、成本更低、服务更好。 以家电制造业为例,创新产品大量涌现,80%的旺销产品生命周期不超过3年,相似产品竞争激烈,抢上市时间、拼价格,愈演愈烈;汽车制造业每年有数以十计的新车型面市,上市时间1824个月,成本每年降低约10%,服务质量无故障等等;IT制造业更是在“摩尔定律”主宰下每18个月翻一番……创新产品对企业成长的贡献率达到50%! 制造业在我国GDP中占到34%,从业人员占工业从业人员的90%,是我国重要的支柱产业。随着我国综合国力的进一步增强和加入世界贸易组织(WTO),我国经济全面与国际接轨,大批跨国企业抢滩登陆在国内高起点设厂、将生产加工向中国大陆转移;国内制造企业更是背水一战,大举通过信息化、广泛应用现代制造技术积极参与国际竞争。我国正逐步成为全球最重要的制造业基地之一。 但是,对于我国制造业企业来讲,却面临两种不同的命运:或者成为全球制造链上“三来一补”的加工车间,或者成为拥有自主核心能力与自主品牌的全球制造中心;或者成为“知识经济”,或者成“劳力”和“资源”经济,两者在国际化市场上的价值分配、竞争地位与发展空间上存在根本性差异。 目前我国已经是全球最大的电视机、电冰箱、空调、影碟机、微波炉、自行车、热水器等家电产品及计算机配件产品制造基地;而且在大到飞机、汽车部件,小到打火机、节能灯,广到服装鞋帽等等的工业品方面,“中国制造”都达到了不俗的规模和层次。但是与当前国际制造业的发展相比,我国制造业存在较大差距,最突出地表现为制造业企业的产品创新能力差、市场响应效率低、自主品牌实力弱,核心竞争力严重不足。 在国际市场上鲜见贴有中国自主品牌的产品,大多以OEM贴牌方式成为外国货;即使是自主品牌产品出口,也因设计创新不足、附加价值不高,“猪肉卖成豆腐价”等等。由于产品创新水平低下、自主核心能力不足,“中国制造”正在沦为“知识经济”模式下全球制造链下游的资源和劳务“车间”。与国外跨国公司依靠产品创新与市场创新赚取的成倍超额利润相比,中国这个“制造车间”却只能拿到1%2%的微薄“辛苦费”。 同时随着加入WTO,我国国内市场已快速开放为国际市场。由于核心竞争能力不足,“中国制造”不仅在参与国际竞争方面面临挑战,而且已经在丧失国内市场上的发展机会与利润空间。 创新是民族的灵魂,更是企业发展的不竭动力。只有具备持续产品创新能力的企业,才能真正在激烈竞争的市场上获得优势。一般来说5000个产品创意中往往仅仅只有一二个产品真正拥有市场前景和商业价值。如果一个企业能够做到5000个产品创意中有5个适销产品必然能够带来巨大的市场优势。具有创新能力的企业要比其竞争者多出两倍的产品创意、三倍的新产品开发并由此获得两倍以上的新产品成功率。 并不是具有产品创新能力的企业人员的素质更高或工作更努力,关键在于人·产品创新与协同管理:他们知道如何更好地使用信息化手段、如何更好地利用信息与知识、如何更好地打破隔阂进行协同,从面释放出信息化的巨大力量;在同等时间周期与资金预算下,能够完成竞争者三倍以上的新产品开发(如图2所示)。 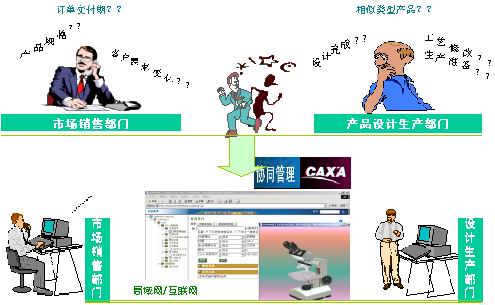 图2产品创新过程中实现产品信息的良好沟通和利用 (未完待续) |
 | |
|